Scale up Process
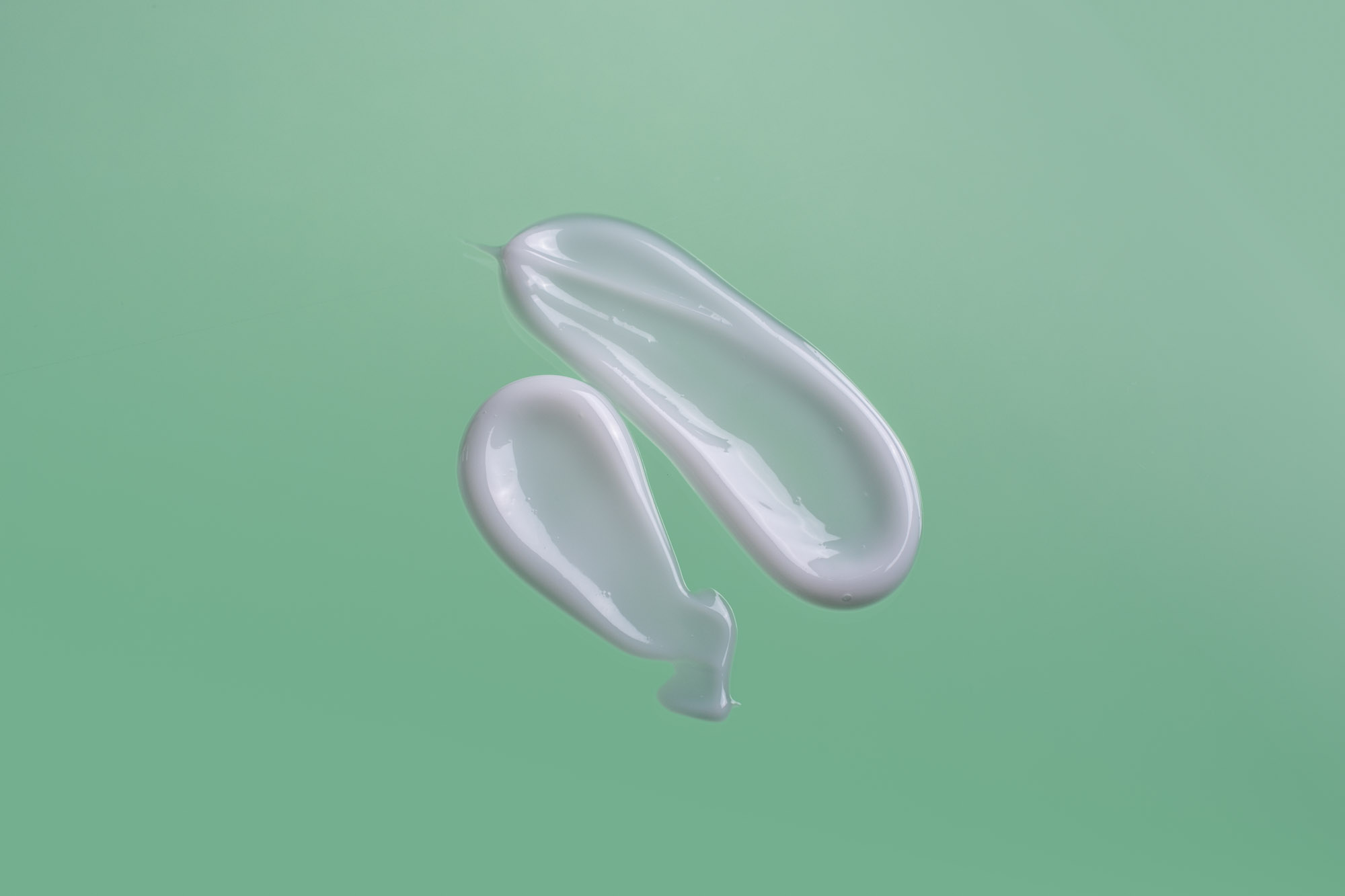
In the development of cosmetic products, it is crucial to introduce the laboratory sample into production settings to ensure its safe and consistent manufacturing. This process involves the scale-up phase, where progressively larger batch sizes are employed during pilot productions. This ensures that the final product replicates the characteristics of the sample created during product development.
Scaling up can be done by increasing the size tenfold or up to twenty times. For instance, if a 100-gram sample is produced, the next step would be a one-kilogram sample, followed by a 10-20 kg batch, and finally, the final production size.
Pilot productions are also necessary to mitigate risks. If a sample fails to yield the same results as the previous one, production can be repeated to ensure consistent quality. This risk reduction is achieved by identifying and rectifying issues early on in the process.
During the scale-up process, the physical parameters and stability of the sample must be thoroughly examined.
Scaling up is most efficient when different sized equipment utilizes the same technology.
Measurement uncertainty can also introduce variability into the final product. With small batches, even highly precise scales can yield significant deviations. This variability can be eliminated through the scale-up process.
Upon completion of the scale-up process, the final batch size, production documentation, and physical parameters are established. This allows for the product's introduction into mass production and the evaluation of manufacturing quality.
Additional Points:
The scale-up process should be documented in detail to ensure consistency and reproducibility.
Analytical testing should be conducted throughout the scale-up process to monitor product quality.
Any deviations from the expected results should be investigated and resolved promptly.
A well-defined scale-up process is essential for ensuring the successful transition of cosmetic products from lab to market.