Extrusion Blow moulding
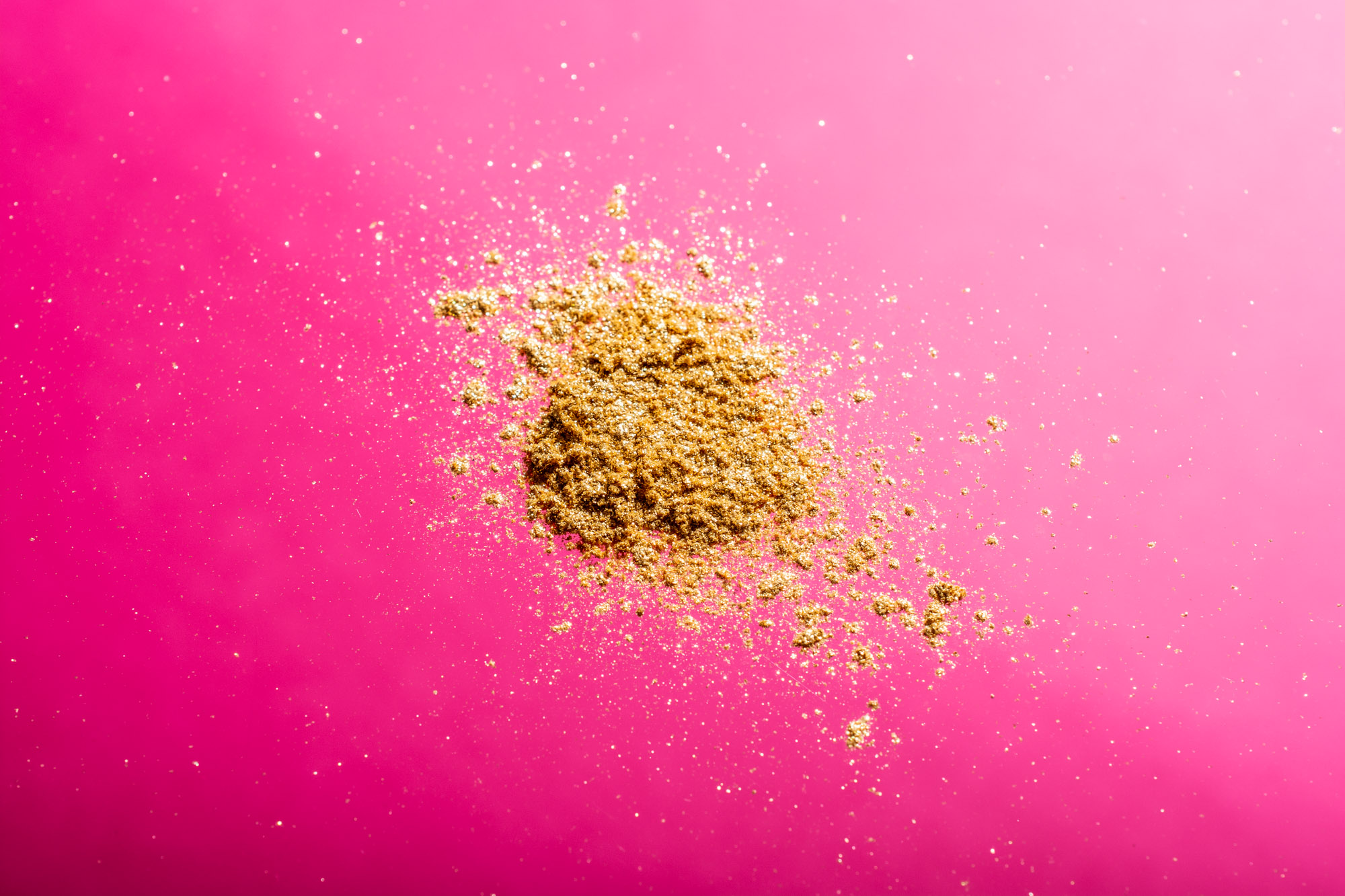
Extrusion Blow Moulding is the process of manufacturing plastic bottles by melting plastic resin and extruding a tube which is them clamped inside two halves of a water-cooled mould.
This tube of plastic is then inflated using pressurized air to the shape of the cavity. While inside, the plastic will freeze off to the shape as it is forced against the inside. The mould will then open, releasing the bottle so that the process can be repeated.
One of the many benefits of the extrusion blow moulding process is the flexibility to change the necks without having to change the entire mould. This customizable solution enables customers to use differing neck fitments on the same bottle mould, eliminating the need for a completely new mould each time, which can prove more cost effective.
What are the advantages of this process?
Extrusion blow moulding is a highly versatile process that can provide unique shapes, sizes and neck types, using a variety of plastics. This versatility gives an overwhelming advantage over the bottle manufacturing processes.
One of the most common resins used in blow moulding is HDPE (high density polyethylene). Although opaque in its natural state, a high gloss feel and appearance can be achieved too.
For a squeezable feel, MDPE (medium density polyethylene) can be used for products such as creams and lotions.
Key advantages:
- Offers good resistance to alcohol, acids and alkalis
- Produces bottles with high stiffness
- Allows forn interchangeable neck moulds
- Easily recycled
- Can be moulded to produce complex shapes and sharp contours