Oil in Water Emulsions (O/W)
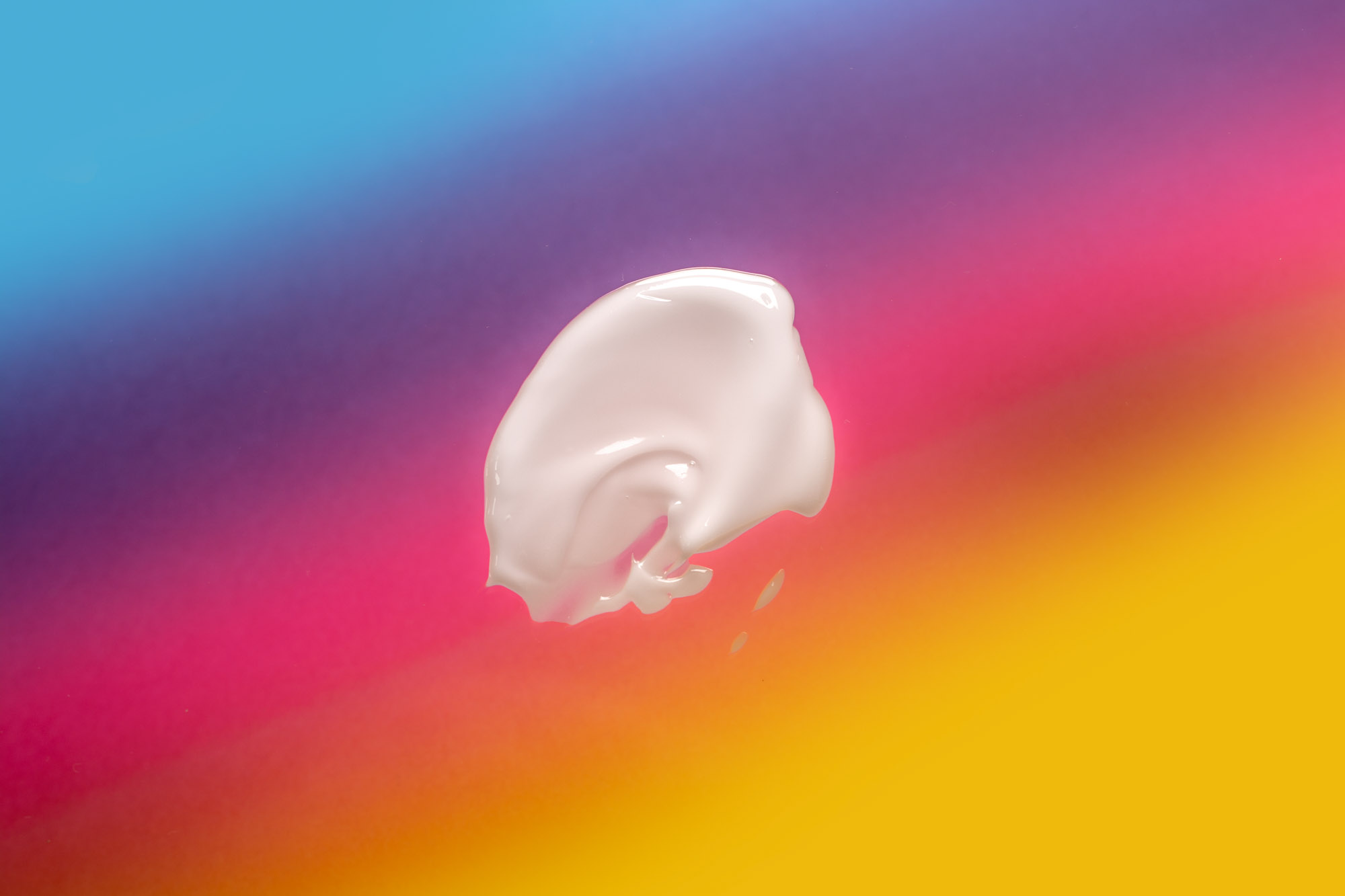
Oil-in-water emulsions typically contain 10 to 35% oil phase, and a lower viscosity emulsion may have an oil phase reduced to 5 to 15%. Water in the external phase of the emulsion helps hydrate the stratum corneum of the skin. This is desirable when one desires to incorporate water-soluble active ingredients in the vehicle. Oil droplets in emulsions have a lower density than the phase they are suspended in; to have a stable emulsion it is important to adjust the specific gravity of the oil and water phases as closely as possible.
Viscosity of the water phase (external phase) may be increased to impede the upward migration of the oil particles. Addition of waxes to the oil phase will increase specific gravity but have a profound effect on the appearance, texture, and feel on application to skin of the product. Increasing water-phase viscosity is one of the most common approaches.
Natural thickeners (alginates, caragenates, xanthan) and cellulosic (carboxymethyl cellulose) gums are used for this purpose.
Carbopol resin is perhaps the most popular gum thickener for contributing towards emulsion stability, especially at higher temperatures. The addition of a fatty amine to a Carbopol resin will further enhance stability by strengthening the interface of the water and oil phases through partial solubilization into the oil droplets. Electrolytes and cationic materials will have a destabilizing effect on anionic sodium carboxymethyl cellulose and should not be used together. Veegum, an inorganic aluminum silicate material, is also commonly used to thicken emulsions. Carbopol and Veegum may be used together to modify the characteristic draggy feel of Carbopol when used at the higher levels.
Emulsifier blends with HLBs ranging from 7 to 16 are used for forming o/w emulsions. In the blend, the hydrophilic emulsifier should be formulated as the predominate
emulsifier to obtain the best emulsion. A popular emulsifier, the glycerol monostearate and polyoxyethylene stearate blend is self-emulsifying and acid-stable. Emulsifiers are called self-emulsifying when an auxiliary anionic or nonionic emulsifier is added for easier emulsification of the formulation. Formulating with self-emulsifying materials containing nonionic emulsifiers permit a wide range of ingredient choice for the formulator, especially with acid systems. In alkaline formulations, polyoxyethylene ether–type emulsifiers are preferred with respect to emulsion stability.
An alternative to glycerol monostearate self-emulsifying emulsifier is Emulsifying Wax, National Formulary (NF). This emulsifier, when used with a fatty alcohol will form viscous liquids to creams depending on the other oil-phase ingredients used. Use levels may vary from 2 to 15%; at lower levels a secondary emulsifier such as the oleths or PEG-glycerides will give good stability. This system is good for stabilizing electrolyte emulsions or when other ionic materials are formulated into the vehicle. Polysorbates are o/w emulsifiers, wetting agents, and solubilizers often used with cetyl or stearyl alcohol at 0.5 to 5.0% to produce o/w emulsions.
Source: Handbook of Cosmetic Science and Technology - André O. Barel, Marc Paye, Howard I. Maibach